HPDC Heat Treatment
Pioneering a new process
Innovations in Die Casting Heat Treatment
Heat treated high pressure die castings are rapidly being introduced into standard car bodies where lightweight strength is needed. As these castings continue to gain acceptance in production vehicles, CEC continues its industry-leading role in providing the testing and machinery to produce these castings with minimal blistering and distortion.
The majority of automotive manufacturers who are serious about integrating heat treated HPDC components into their models are currently running, or have run, their tests with CEC. As a result of these tests, many die cast production parts are being run through CEC’s innovative HPDC furnace systems right now. These systems feature the improvements that we have developed, specifically for complex structural die cast parts, in the areas of casting support via fixtures, uniform quenching systems, furnaces, and alloy/ part tailored recipes.
With the largest collection of tests on treated high pressure die castings in the world, we are able to design an optimal recipe, quench process, and fixture for each component. Using GOM 3D scanning, we measure parts before and after heat treatment to ensure that parts are consistently meeting requirements for distortion while maximizing properties.
CEC is the first furnace company to seriously push HPDC technology into real-world production, and the first to design this technology into a dependable system. We are the exclusive licensee & supplier for all CSIRO-developed HPDC teat treatment technology for NAFTA and the EU.
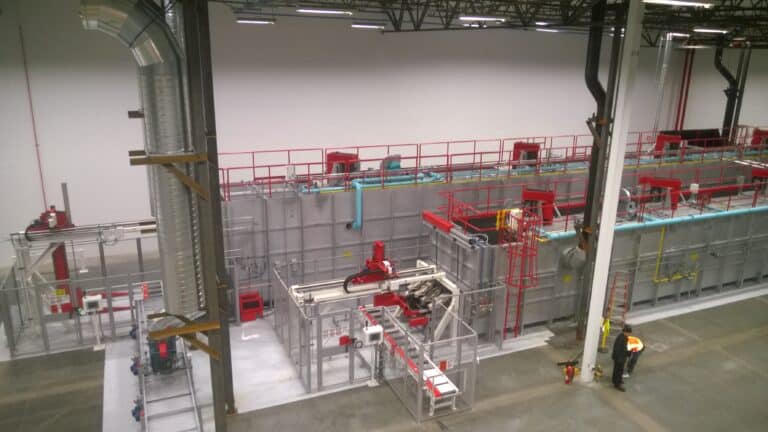
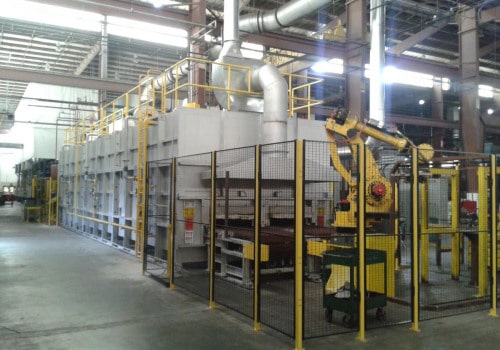
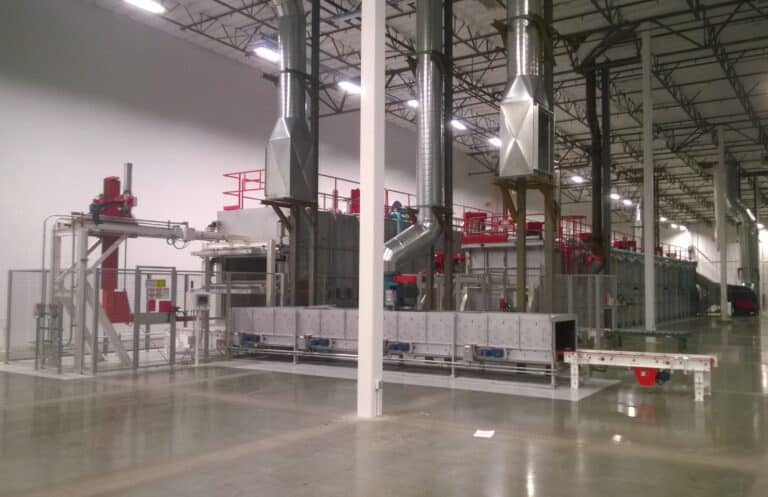
CHOOSE THE MOST EXPERIENCED HPDC PARTNER
CEC has the world’s largest collection of tests on heat treated die castings.
We have been involved with die casting heat treatment since the beginning.
Designing the first HPDC Treatment Systems
CEC’s relationship with CSIRO began shortly after Roger Lumley & others performed the first practical testing of this technology. Since then, hundreds of HPDC heat treatment tests have been run by CEC. We have developed our own series of machinery designs to optimally heat treat complex structural die castings with minimal distortion or blistering.
We provide the most comprehensive testing in the world in this area, drawing from the results of all CSIRO tests and our own extensive tests on a large variety of aluminum alloys. Using the latest technology in our large in-house testing facility to measure part properties and distortion after treatment, we arrive at optimal time and temperature recipes that yield superior properties with an extremely low scrap rate.
As a new technology, treated die castings can cause a lot of problems in production. Recipes, quench systems, fixtures, and the furnaces themselves all need to be developed with a thorough understanding of the part’s geometry, target properties, and alloying constituents.
Thorough testing and expert system design is the key to stable production and dependable part properties. In several cases, we have been called in by car companies to re-engineer and overhaul existing HPDC T7 treatment systems that our competitors have installed because of poor properties, unacceptably high scrap rates, or both.
We encourage you to talk to a CEC expert in HPDC heat treatment before you purchase from another company that does not specialize in this challenging area. You can find more information on HPDC heat treatment in the following sections below, or by contacting us via the chat box to set up a private presentation.
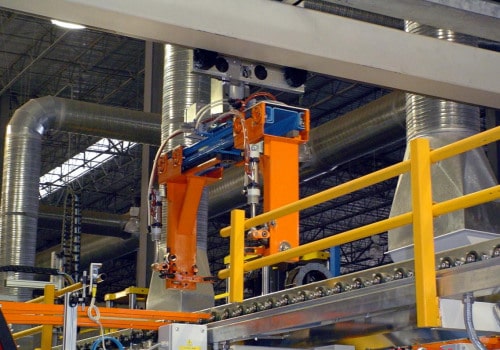
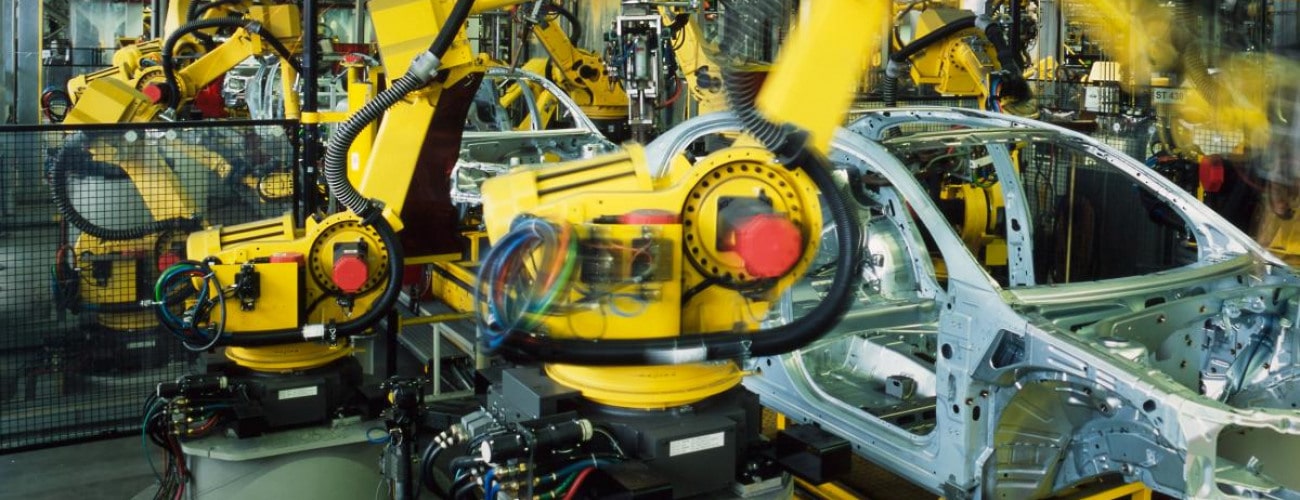
More Information on HPDC Heat Treatment
What is HPDC?
High Pressure Die Casting, in which molten aluminum is injected into a metal die, now accounts for more than half of all aluminum castings worldwide.
This manufacturing method has shown to be particularly suitable for making complex part shapes for automobiles. These castings are often used as sheet or extrusion connectors to tie together portions of all aluminum car space frames (chassis) which are finding broader application in high-end cars.
Die castings used in vehicles include:
Engine blocks
Shock tower housings
Spring frame castings
Transmission housings
B-pillar castings
Pressure from environmental regulations has contributed to increased interest in die castings for automobiles. Mandates to reduce tailpipe emissions all over the world have driven vehicle designers away from heavy iron and steel components, and as the trend continues, even away from wrought and cast aluminum products towards lightweight die cast components. Further regulatory guidance has also driven automobile manufacturers to meet minimum recyclable requirements. Here aluminum components, and HPDCs in particular are well suited to comply with standards as historically over 95% of die castings are produced with secondary (recycled) aluminum alloys.
The biggest problems that die castings face, as they become more popular in automotive production, have been the same for many years. Because of how they are manufactured, die castings contain a much higher level of inclusions in the form of air, steam, decomposing die lubricants, and hydrogen that become trapped in the casting as the die fills. Typical levels of inclusions (measured in cm^3 of gas content relative to casting weight) are five to ten times greater in high pressure die castings than observed in sand, permanent mold, low pressure, and vacuum die casting methods.
The presence of these inclusions in high amounts has prohibited successful traditional heat treating of die castings; where solution time is often greater than one hour. Under traditional long heat treatments, even higher quality HPDC’s with lower than typical inclusion levels can blister and deform as the pockets of air within the castings heat up at a different rate than the aluminum of the casting and cause stresses and blisters as they escape. Traditional, long-dwell time heat treatment of die castings can, because of this issue, do more harm than good.
New CEC and CSIRO recipes, stipulating shortened treatment times and modified quenching rates, have been developed to overcome the issues commonly associated with heat treating of die cast components. The die castings that can benefit from a CEC recipe must still meet certain maximum allowed standards for inclusion however. HPDCs that contain very high levels of inclusions cannot benefit from any heat treatment. But, thanks to the advancements in die casting production, most manufacturers are now able to produce die castings of a high enough quality that heat treating is a viable option.
High pressure die casting quality continues to improve on the casting side. Computer modeling of the flow of molten aluminum through the feed(s) and into the die allows casting engineers to highlight and prevent areas where high turbulence is created. Variable feed gating & variable flow of molten aluminum enables engineers to change the speed of the aluminum when it reaches key areas within the die, again leading to smoother fills & less inclusions. Advancements in die lubricants have also contributed to more repeatable casting processes.
Die castings offer many advantages to a large volume casting manufacturer. HPDC’s offer:
High dimensional accuracy even with thin wall parts.
Smooth cast surfaces which require fewer secondary machining operations.
Low per-part cost when high volume is called for relative to sand and semi-permanent casting methods.
The possibility of heat treatment of high pressure die castings promises to bring these benefits to a greater range of parts as more structural parts, particularly in automotive applications, are poised to benefit from these developments. In general, these technologies will continue to impact automotive design as knowledge of them becomes more ubiquitous. Approximately 3% of the weight of an aluminum component can be reduced for every 10% improvement in yield stress or design stress. With CEC & CSIRO recipes achieving 100% yield strength improvements, with no loss to elongation as compared to as cast, significant weight savings can be realized through HPDC heat treating.
CEC has performed thousands of tests to improve properties of low pressure and high pressure die castings. Our T4, T6 or T7 heat treatment recipes allow the part size and weight to be dramatically reduced due to improved materials properties. Conventional die cast parts have very high gas content which prevents traditional heat treatment. New processes allow heat treatment and implementation of cores in a broad array of high pressure die castings.
Recent Developments in HPDC Heat Treatment:
CEC has developed significant improvements to fixturing and testing methodologies for die casting heat treatment. The following sections on fixtures, trays, and testing methodology may be expanded for further reading.
Fixtures/ Trays for Die Cast Components
CEC has spent the last 6 months developing better heat treatment fixtures and trays for T6 and T7 applications for Aluminum high pressure and high vacuum die castings.
The purpose of the studies included:
- Making accurate fixtures and trays at a lower cost
- Seeing what various fixture and tray designs allowed less casting distortion
- Designing the fixture to focus heating and quenching air on the critical casting surfaces
- Assuring uniform heating and cooling rates for large production systems so that solution times were optimized
- The tray conveys the casting through the heat treatment system and supports the fixture. The fixture touches and supports the casting.
- Many fixture designs were studied and heat treatments to a T6 or T7 temper were performed.
CEC High Pressure Die Casting Testing Methodologies
CEC uses dimensional deviation scanning technologies, along with traditional methods of casting quality analysis to determine optimal recipes for die cast parts. Initially, CEC scanned the casting with a GOM machine to measure the casting dimensions and then the casting was heat treated with various fixture designs. The result was a distortion analysis that related to the fixture. After the heat treatment was performed the casting was again scanned and the deviation of before heat treatment and after was compiled into a color defined dimensional deviation image and deviation distribution bar chart.
We believe that CEC trays and fixtures are better thought out, tested and lower cost than our competitors. Our T6 and T7 systems are fully automated and allow 2D casting or tray tracking to be added via Cognex or SICK scanners and data to be stored in a SCADA system.
Please call today or use the chat box below to learn more about how CEC and CSIRO technologies can greatly reduce your casting distortion and improve mechanical properties. CEC has developed mechanisms and processes that will allow our customers to leap ahead of rival foundries and car companies with stronger HPDC components. We are currently sharing this new group of technologies with companies on a private basis.
CEC has lists of test results for almost 100 of the most common alloys used in die casting automotive structural castings. CEC recently performed tests on approximately 75 castings to confirm mechanical properties that are achieved when using short cycle solution heat treatment with a stepped thermal setting. The tests were performed at the CEC facility in Georgia and an outside laboratory was used to confirm the mechanical properties of the die castings.
One recent test featured shock-towers for a European luxury car manufacturer. Casting strength was improved by 80-110% with a full (heat-up and soak) solutionizing time of 42 minutes maximum followed by a conventional artificial ageing time.
Other casting heat treatment cycles have been developed for shock towers and battery support castings recently. These castings are now in use in luxury German electric cars.
CEC has tested many castings for T4, T6, T7 tempers in the thin structural casting area. Of course, some thicker and heavier castings have also been run, such as engine blocks. Upon request, we can provide lists of casting descriptions tested in optimized temper processes for lowest cost and pollution.
CEC brings a unique and expert opinion to casting processing. Please give us an opportunity to explain our perspective, we would love to learn together with you. Often, our testing background over the last 30 years on aluminum castings will allow us both to take some short cuts that still result in improved processes for your casting application.